Share This Guide
Are you struggling to find out what’s wrong with your AC? Has your liquid line started getting cold out of nowhere?
That might make you relentlessly think about why my liquid line is cold.
The most frequent reason behind your liquid line being frozen is restricted airflow. Your liquid line will stop working when pollutants block your filter drier. Other common reasons include a stuck solenoid valve and TXV being partially closed. Moreover, a low level of refrigerant can cause this issue too.
Well, those were the reasons that might disturb your liquid line. But no worries! I’ve mentioned all the tips and tricks on how to fix these issues.
Main Reasons Why Your Liquid Line is Cold and Their Solution!
Often we mistake the liquid line restriction for the undercharging of refrigerant. For this, when AC works during the day but not at night it might be a liquid line problem. But it’s more of a refrigerant charge problem. Here are the reasons why your liquid line is cold.
Causes of Restrictions
This table summarizes the common causes of liquid line restrictions.
Cause | Description |
---|---|
Too much oil in the system | Excess oil can cause the TXV to become restricted. |
TXV adjusted too far closed | Over-adjustment can restrict refrigerant flow. |
Plugged inlet screen on TXV | Debris can block the TXV inlet screen. |
Sludge from compressor burnout | Byproducts of a burnout can clog the system. |
Partial TXV orifice freeze-up | Excessive moisture can freeze and block the TXV. |
Foreign material in TXV orifice | Contaminants like dirt and debris can cause blockages. |
Oil-logged TXV | Refrigerant flooding can cause oil logging. |
Restricted liquid line solder joint | Poor soldering can create restrictions. |
Kinked liquid line | Physical damage can restrict flow. |
Receiver outlet valve partially closed off | Improper valve settings can restrict flow. |
Wax build-up from incorrect oil | Wrong oil can lead to wax build-up and restrictions. |
Manufacturer’s defect in the valve | Faulty valves can cause restrictions. |
Insufficient Airflow: How It Causes Your Liquid Line to Get Cold
The primary function of the evaporator coil in your AC system is to absorb heat from the air. When airflow is restricted, the coil cannot effectively take in heat, leading to condensation that can freeze on the coils. This results in a cold liquid line. Several issues can contribute to poor airflow, such as a dysfunctional blower fan, clogged air filters, or faulty ductwork.
Common Causes of Insufficient Airflow:
- Clogged Air Filters: Dust and debris can accumulate on air filters over time, blocking airflow. This is one of the most common causes of insufficient airflow.
- Dysfunctional Blower Fan: If the blower fan is not working correctly, it cannot push enough air over the evaporator coils.
- Faulty Ductwork: Leaks or blockages in the ductwork can impede airflow, preventing the AC system from operating efficiently.
Steps to Identify Airflow Problems:
- Inspect Air Filters: Check your air filters regularly. If they are dirty or clogged, replace them. This simple step can significantly improve airflow.
- Check the Blower Fan: Ensure the blower fan is operating correctly. Listen for unusual noises or vibrations that might indicate a problem.
- Examine Ductwork: Inspect your ductwork for any visible signs of leaks or blockages. Repair any leaks and remove obstructions to ensure proper airflow.
Solution to Insufficient Airflow:
- Thaw the Evaporator Coil:
- Turn off the AC system and allow the evaporator coil to thaw. This process can take 12 to 24 hours, depending on the extent of the ice buildup.
- Alternatively, switch to a fan-only mode. This will help warm air circulate over the coils, speeding up the thawing process.
- Remove Ice and Water:
- Place containers or towels to catch water as the ice melts. This prevents water damage to other components of your AC system.
- Clean or Replace Air Filters:
- Regularly clean or replace air filters to maintain optimal airflow. Consider using high-quality filters to capture more dust and debris.
- Maintain the Blower Fan and Ductwork:
- Schedule regular maintenance checks for your blower fan to ensure it operates efficiently.
- Inspect ductwork periodically and repair any leaks or remove blockages promptly.
Preventive Measures:
- Regular Maintenance: Schedule regular HVAC maintenance to keep your system in top condition.
- Air Filter Replacement: Replace air filters every three months or as recommended by the manufacturer.
- Ductwork Inspection: Have your ductwork inspected and cleaned annually to prevent airflow issues.
By addressing these airflow problems, you can ensure that your AC system operates efficiently, preventing the liquid line from becoming excessively cold and maintaining a comfortable indoor environment.
Filter Drier is Jammed Up
The average lifespan of a liquid line filter drier is limited. It’ll ultimately clutter up from all the contaminants it screens out of the refrigerant.
Source: qualitycomfortfl.com
The moisture sieve beads, however, will finally achieve concentration. They can only retain this much water. It can also make a noise like the one it makes during a power outage.
Common Causes of a Clogged Filter Drier:
- Accumulation of Contaminants: The filter drier traps moisture and debris, which can build up over time, reducing its effectiveness.
- Moisture Saturation: The desiccant beads inside the filter drier absorb moisture. Once they reach their capacity, the filter can no longer function properly.
- Blocked Air Filters: Clogged air filters can reduce airflow, causing dirt and contaminants to accumulate in the refrigerant circuit, which can then clog the filter drier.
Signs of a Clogged Filter Drier:
- Noise: A clogged filter drier can produce unusual noises, similar to the sound during a power outage.
- Reduced Airflow: Insufficient airflow can result from a clogged filter, affecting the evaporator coils’ ability to absorb heat.
Steps to Identify Filter Drier Issues:
- Inspect for Noise: Listen for any unusual noises coming from the filter drier, which could indicate clogging.
- Check Airflow: Assess the airflow from the AC unit. Reduced airflow might point to a clogged filter or filter drier.
Solution to a Clogged Filter Drier:
- Replace the Filter Drier:
- Purchase a Quality Filter Drier: Select a reliable filter drier compatible with your AC system. Products like the PowerWell Refrigerant Filter Drier or Appli Parts Refrigerant AC Filter Drier are good options.
- Follow Replacement Tutorial: Use a step-by-step guide to replace the filter drier properly. Ensure you have the necessary tools and follow safety precautions.
- Inspect the Refrigerant Circuit:
- Check for Contaminants: Thoroughly inspect the entire refrigerant circuit, including the evaporator and condenser coils, to identify the source of contaminants.
- Seal Leaks: Look for holes or weak connectors in the circuit and seal them to prevent future clogs.
- Maintain Air Filters:
- Regular Cleaning: Clean your air filters regularly to prevent dirt from entering the refrigerant line.
- Timely Replacement: Replace air filters every three months or as recommended by the manufacturer. Consider high-quality options like Simply by MervFilters or Filtrete AC Furnace Air Filters.
Preventive Measures:
- Regular Maintenance: Schedule routine maintenance checks to keep your AC system in optimal condition.
- Monitor Filter Drier: Keep an eye on the filter drier’s condition and replace it when necessary to prevent clogs.
- Clean Air Filters: Ensure air filters are clean and replaced regularly to maintain proper airflow and reduce the risk of contamination.
And guess what? These are the filter driers that I use for my own clients.
Products | Compatible Refrigerants | Price |
PowerWell Refrigerant Filter Drier | HFC , CFC , HCFC | Order Now |
Appli Parts Refrigerant AC filter drier | r1234yf, r134a, r290, r22, r407c, r404a, r507a, r600 | Order Now |
Now you have the best filter drier, you should be able to change your AC’s filter drier. Check out this tutorial and follow it properly to change the filter drier perfectly.
Low Level of Refrigerant
A sufficient amount of refrigerant is required for conditioners to operate properly. AC units are designed to operate in a loop system. It means that refrigerants will not get lost out of anywhere.
Therefore, low refrigerant means a leak or absence of charge causes the issue. When there is a refrigerant leak, the pressure of the refrigerant suffers a downfall.
Common Causes of Low Refrigerant:
- Refrigerant Leaks: Leaks can occur in various parts of the AC system, such as the coils, connectors, or refrigerant lines.
- Incomplete Charge: Sometimes, the AC system might not be charged properly during installation or maintenance, leading to insufficient refrigerant levels.
Signs of Low Refrigerant:
- Reduced Cooling Efficiency: The AC might not cool the space as effectively as before.
- Hissing or Gurgling Sounds: These sounds near the outdoor unit can indicate a refrigerant leak.
- Frozen Evaporator Coils: Low refrigerant levels can cause the evaporator coils to freeze, leading to a cold liquid line.
Steps to Diagnose Low Refrigerant Issues:
- Use a Refrigerant Leak Detector:
- Recommended Tools: Elitech WJL-6000S Freon Leak Detector and Aprvtio Refrigerant Leak Detector with LED Light are effective tools for identifying leaks.
- Detection: Check for leaks in the refrigerant lines, connectors, and coils. The detector will help you pinpoint the exact location of the leak.
- Listen for Unusual Sounds:
- Hissing or Gurgling: Turn off the AC and listen for any hissing or gurgling sounds near the outdoor unit, indicating escaping refrigerant.
Solution to Low Refrigerant Levels:
- Fix the Leaks:
- Seal the Leaks: Once you identify the leak, use duct tape (UL 723 or UL 181) or a more permanent sealant to fix the leak. Ensure the repair is airtight to prevent future leaks.
- Professional Help: If the leak is significant or in a difficult-to-reach area, contact a professional HVAC technician to repair it.
- Recharge the System:
- Proper Charging: After fixing the leak, the AC system needs to be recharged with the correct amount of refrigerant. This ensures the system operates efficiently.
- Professional Service: It is recommended to have a professional recharge the system to ensure it is done correctly and safely.
Preventive Measures:
- Regular Maintenance: Schedule routine maintenance checks to ensure all components of the AC system are in good condition and to catch any potential leaks early.
- Monitor Refrigerant Levels: Regularly check the refrigerant levels and pressures in the system to ensure they remain within the manufacturer’s specified range.
- Seal Connections: Ensure all connections in the refrigerant circuit are secure and free from leaks.
You can choose any duct tape between ul 723 and ul 181 to fix the leaks.
When the TXV Gets Stuck
The Thermostatic Expansion Valve (TXV) regulates the flow of refrigerant into the evaporator coil. If the TXV gets stuck, it can restrict the refrigerant flow, causing the liquid line to become cold. Common causes include overheating, oxidation reactions, and loss of refrigerant from the powerhead, cap tubing, or bulb assembly.
Common Causes of a Stuck TXV:
- Overheating: Excessive heat can cause the TXV to malfunction or become stuck.
- Oxidation: Rust inhibitors in the system’s initial oil charge can react with oxygen, leading to the TXV getting stuck.
- Refrigerant Loss: Loss of refrigerant from the powerhead, cap tubing, or bulb assembly can cause the TXV to become stuck.
Signs of a Stuck TXV:
- Cold Liquid Line: A stuck TXV can lead to an excessively cold liquid line.
- Inconsistent Cooling: The AC may provide inconsistent cooling, with fluctuating temperatures.
Steps to Diagnose TXV Issues:
- Check for Temperature Fluctuations:
- Inconsistent Cooling: Monitor the cooling performance of your AC. Inconsistent temperatures can indicate a stuck TXV.
- Inspect the TXV Components:
- Visual Inspection: Look for signs of damage or wear in the powerhead, cap tubing, and bulb assembly.
- Listen for Unusual Sounds: A stuck TXV might cause unusual sounds due to restricted refrigerant flow.
Solution to a Stuck TXV:
- Add a Lubricant Additive:
- A/C ReNew: Start by adding a lubricant additive such as A/C ReNew to the system. This can help free up the TXV.
- Improvement Timeline: After adding the additive, run the system for a few hot and cold water sessions. It may take up to 48 hours of standard air run time to see improvement.
- Engage the TXV Bulb:
- Hot and Cold Water Sessions: Dip the TXV bulb in hot and cold water multiple times to help free the valve.
- Monitor Performance: Continuously monitor the system’s performance to ensure the TXV is functioning correctly.
- Consult the Manufacturer:
- Chemical Use: Before applying any chemicals to the refrigeration cycle, consult with the manufacturer to ensure warranty compliance and safety.
Preventive Measures:
- Regular Maintenance: Schedule regular maintenance to check the TXV and other components for signs of wear or damage.
- Monitor System Performance: Regularly monitor the cooling performance and temperature consistency of your AC system.
- Use Quality Refrigerants: Ensure that the refrigerants and additives used in the system are of high quality to prevent oxidation and other issues.
Diagnostic Measurements and Values
Measured and Calculated Values Table
Parameter | Liquid Line Restriction | Undercharged System |
---|---|---|
Measured Values | ||
Compressor Discharge Temperature | 215°F | 195°F |
Condenser Outlet Temperature | 70°F | 78°F |
Evaporator Outlet Temperature | 30°F | 10°F |
Compressor Inlet Temperature | 60°F | 50°F |
Ambient Temperature | 70°F | 70°F |
Refrigerated Space Temperature | 30°F | 20°F |
Compressor Voltage | 230v | 230v |
Compressor Amperage | Low | Low |
Low-Side (Evaporator) Pressure | 1.8 psig (minus 10°F) | 3.94 inches Hg (minus 20°F) |
High-Side (Condensing) Pressure | 95 psig (85°F) | 86.4 psig (80°F) |
Calculated Values | ||
Condenser Split | 15°F | 10°F |
Condenser Subcooling | 15°F | 2°F |
Evaporator Superheat | 40°F | 30°F |
Compressor Superheat | 70°F | 70°F |
Diagnostic Tools
This table lists recommended tools for diagnosing liquid line restrictions and other AC system issues.
Tool | Purpose |
---|---|
Refrigerant Leak Detector | Identifies refrigerant leaks in the system. |
Thermometer | Measures temperatures at various points in the system. |
Pressure Gauges | Measures low-side and high-side pressures. |
Multimeter | Checks voltage and amperage of the compressor. |
Sight Glass | Allows visual inspection of refrigerant flow and condition. |
Flushing Agent | Cleans the refrigerant circuit to remove contaminants. |
Moisture Absorbing Additives | Prevents moisture accumulation in the system. |
FAQs
What causes the liquid line to stop in the first place?
Insufficient Airflow can cause your liquid line to stop working. Even in the summer season, this can result in your liquid line freezing. Coolant will not receive sufficient heating to be discharged indoors due to poor ventilation. And this will lead to a frozen line.
How can I understand if my air conditioning duct is frozen?
Aside from visible frost on any area of your HVAC machine, an absence of chilly air is an indicator of a frozen AC unit. If you place your palm in front of your supply vents and you feel hot air flowing out. You most likely have frost in the system.
How long does an AC coil last?
If properly maintained, an evaporator coil will generally last 8 to 14 years. This is the average shelf life of an evaporator coil. It is quite similar to the life expectancy of an AC. Your coils will have a shorter life if your unit isn’t carefully maintained.
Final Thoughts
That was all our take on why my liquid line of AC is cold. We hope that you have found your answer to why your liquid line is not working.
A special tip for you would be to always check for your filter dryers. Try to keep them clean and maintain them regularly.
Good luck!
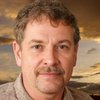
HVAC tech with over 30 years of experience. Retired and doing repair work on the side around Madison County, AL.